Tungsten Carbide Button for Roller Cone Bit
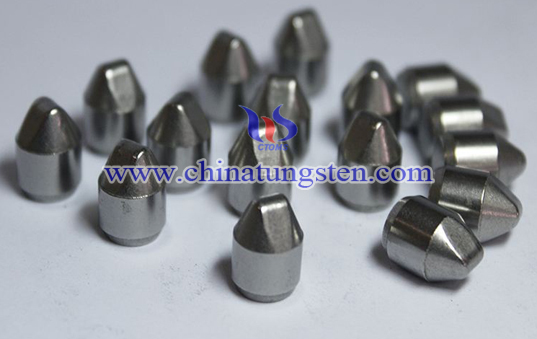
Introduction
A roller cone bit is the most widely used type of drill bit. When the cone bit is working, the hard alloy ball teeth alternately contact the bottom of the well, the rock breaking torque is small, the contact area between the cemented carbide ball and the bottom of the well is small, the specific pressure is high, and it is easy to eat into the formation. The total length of the working edge is large, so it is relatively reduced. abrasion. The roller cone bit can accommodate a variety of formations from soft to hard.
The roller cone bit has been widely used as a tool for drilling rock formations. Significant improvements in drill performance directly reduce drilling costs, especially in the last decade. Two performance indicators, service life and drilling speed, which ultimately determine the extent to which the drill bit affects drilling costs. Increasing the drilling speed and service life of the drill bit is an effective way to reduce the drilling cost, and the use of cemented carbide ball teeth as the main cutting tooth of the roller bit is the best choice. The improvement of the cutting structure mainly focuses on the main cutting tooth structure. For example, in the cemented carbide ball tooth structure, wedge teeth, scoop teeth, partial scoop teeth, and other wear teeth have been invented.
Features
1. The high-strength and high-toughness hard alloy ball teeth are used to improve the impact resistance of the main cutting teeth and reduce the breaking rate;
2. Optimized design of the number of rows of teeth, the number of teeth, the height of the tooth and the unique shape of the alloy teeth, giving full play to the cutting ability and cutting speed of the drill;
3, using a circlip to lock the cone, can withstand high drilling pressure;
4. The inner hole of the cone is inlaid with anti-friction alloy to improve the anti-seizure ability of the bearing;
5. The high-saturated nitrile rubber O-ring seal is used, and the optimized sealing compression improves the reliability of the bearing seal;
6. It adopts the all-rubber oil storage bladder which can limit the pressure difference and prevent the drilling fluid from entering the lubrication system, which provides good lubrication for the bearing system and ensures the normal operation of the “O”-shaped sealing ring and improves the working life of the drill bit;
7. It adopts new grease which can withstand high temperature of 250 °C and low wear, which improves the ability of the bit seal lubrication system to withstand high temperature.