Tungsten Carbide Button for Downhole Drilling
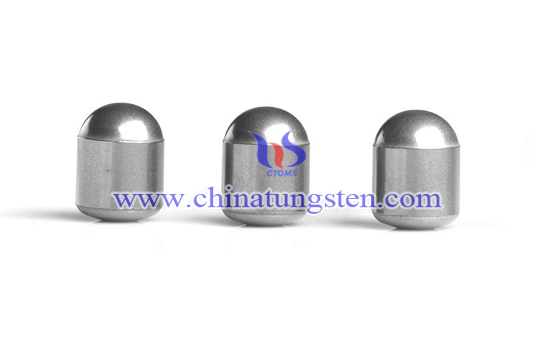
Introduction
DTH drilling refers to the rock drilling method in which the impact mechanism sneaked into the inside of the blasthole. The torque of the slewing mechanism rotates the impactor and the drill bit through the drill pipe. The rock shovel is outside the exhaust gas exit hole of the impactor. Since the impactor of the downhole rock drilling advances with the increase of the hole depth, it is not necessary to connect the long drill rod, so the transmission efficiency of the impact energy is not reduced due to the hole depth.
DTH drills are available in both blade and cylindrical versions. Blade-type drills typically have four wings, three wings at smaller diameters, and the wings are welded with a carbide tip with a corner angle of 110°. The cylindrical bit is a new type of drill developed in the late 1960s. It embeds a certain number of cylindrical carbide teeth on the working end face, and the tip of the tooth is hemispherical or bullet-shaped. Generally, the interference fit is used in the cold press and solid tooth process. Tooth bit has a higher service life and drilling speed, so it has gradually replaced the blade bit. The blade or the column tooth is made of cemented carbide. Containing 89%-92% of tungsten carbide, containing 8%-11% of cobalt, and sometimes adding a small amount of niobium carbide. To improve its impact toughness and wear resistance.
Advantages
Tungsten carbide button have superior wear resistance and impact toughness, and with much higher speed compared with similar products. The button series passivation has a long service life, and its non-wear life is about 5-6 times of the grinding life of the same diameter blade head bit, which is beneficial to save auxiliary working hours, reduce manual labor and speed up engineering.